Revolutionary Energy-Saving Game-Changer: Georgia Pacific’s HPC® EPA ENERGY STAR Win
Key insulation benefits
- Georgia-Pacific wins the EPA ENERGY STAR Award for energy efficiency with HPC® Coating
- HPC® Coating at Naheola paper mill saves $332,000 annually with one digester
- Georgia-Pacific’s commitment to environmental stewardship emphasized exclusively through HPC® Coating
- HPC® Coating reduces heat loss, prevents corrosion, and withstands high temperatures
- Successful HPC® Coating application at Naheola mill leads to broader use in Georgia-Pacific plants
- Potential annual savings across all plants estimated over $20 million
- HPC® Coating dual benefit of insulation and corrosion prevention could save over $40 million per annum
- HPC® Coating insulation coating material gives 13-18 month ROI estimated from savings reported
- Provides exceptional employee personnel protection
- Georgia-Pacific engineers reported completely stops corrosion under insulation
- Groundbreaking insulation technology that revolutionizes industry and environmental benefits
2023 EPA ENERGY STAR Energy Saving Award
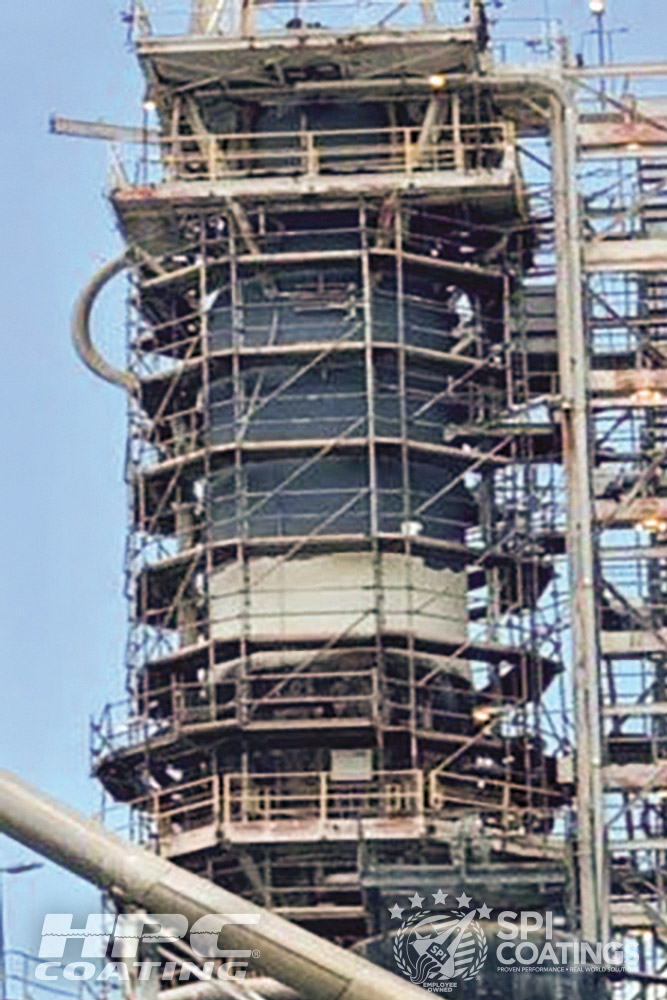
Georgia-Pacific has been recognized by the U.S. Environmental Protection Agency (EPA) for its revolutionary application to energy efficiency with HPC® Coating. SPI Coatings innovative high temperature ceramics insulation coating, HPC® Coating was applied to a Naheola paper mill digester tank at Georgia Pacific which saved $332,000 in annual energy costs, winning the EPA ENERGY STAR Energy Saving Award.
Georgia-Pacific has always shown a commitment to environmental stewardship and continuously improving energy efficiency and identified that HPC® Coating was a clear benefit to all other options in the marketplace. The ENERGY STAR® program recognized the work of Georgia-Pacific, Flint Hills Resources and their parent company Koch Industries for a Top Project at the 2023 ENERGY STAR Industrial Partner Meeting in October 2023. The recognition comes for their efforts to improve energy efficiency, reduce CO2 and reduce corrosion in Koch manufacturing assets.
Innovation of HPC® Coating as a Revolutionary Insulation Coating
Together with Flint Hills Resources, Georgia-Pacific engineers tested a wide range of insulation options to protect manufacturing equipment and found a solution in HPC® Coating that reduces heat loss, prevents corrosion, and can be applied to equipment that operates at temperatures up to 1,200°F / 650°C. HPC is a ceramic based, water-borne insulating coating designed with over seven lightweight, low-density ceramics to insulate in high temperature situations from 100° to 650°C.
It is a thick, closed film thermal insulation coating that works opposite to traditional open film insulation that uses air to slow heat yet also allows air and moisture to transfer. HPC® Coating as a vacuum (hermetically) sealed insulator coating blocks heat loss, saves energy, reduces maintenance, stops CUI (Corrosion Under Insulation), reduces landfill and personnel protection. HPC can also last over 15 years (without abuse) with maximum benefits during that time.
HPC® Coating was first tested by Georgia-Pacific on a condensate receiver at its Naheola paper mill in Pennington, Alabama. The condensate receiver captured excess steam and condensation produced by a paper machine. Georgia-Pacific then moved forward with coating a full digester at Naheola with HPC® Coating in March 2020.
Read the Georgia Pacific News
HPC® Coating offers Multiple Critical Benefits
- Significant Energy Savings: A key benefit of using HPC® Coating in industrial settings is the substantial energy savings it offers, leading to significant cost reductions.
- Corrosion Prevention: HPC® Coating effectively blocks corrosion under insulation (CUI), thereby extending equipment life and reducing maintenance costs.
- Enhanced Safety Improvement: It provides burn protection and personnel safety to employees by reducing surface temperatures.
- Operational Efficiency: HPC® Coating can be applied while equipment is operational, avoiding shutdowns.
- Environmental Impact: Reducing energy consumption contributes to lower emissions, aligning with green initiatives and carbon emissions.
The Use of Digesters for Many Industries
Digesters cook wood chips at high temperatures to obtain the pulp fibers used to make paper products. During the process, the wood chips are loaded into the digester, and chemicals added. The temperature is then raised to around 160°C, and the pressure is increased to several atmospheres. This high temperature and pressure helps to break down the lignin in the wood, which acts as a natural glue, allowing the cellulose fibers to separate.
A digester unit in the context of industries like oil, gas, and energy, is typically a vessel or system where biological decomposition of organic material takes place. This process is commonly used in waste management, wastewater treatment, and biogas production. Digesters break down organic matter, often in the absence of oxygen (anaerobic digestion), to produce biogas, which can be used for energy, and digestate, a nutrient-rich substance used as fertilizer. This aligns well with sustainability and energy-efficient goals in various industries.
The Expensive Impact of Corrosion Under Insulation (CUI)
Corrosion can be caused by traditional and commonly used bulk or wrap insulation in industrial equipment like digesters. CUI occurs when moisture becomes trapped between the insulation and the equipment surface. Over time, this moisture can lead to significant corrosion damage, impacting the integrity and safety of the equipment. The cost of CUI can be substantial, often involving expensive repairs, maintenance, and even equipment replacement. Additionally, there are indirect costs in maintenance, placement, production downtime and safety risks. The exact cost can vary widely depending on the extent of the corrosion, the type of equipment, and the industry sector. In some cases, the annual cost of CUI can reach millions of dollars for a single facility.
HPC® Coating protected the Georgia Pacific digester from corrosion. The Naheola digester had already begun to experience corrosion prior to application, a common issue for digesters of its age. HPC® Coating hermetically sealed the digester to keep out any new moisture, so when some of the HPC® Coating was removed in 2022 to allow for repairs to the digester, there was no evidence of new corrosion.
The choice of operating temperatures for digesters depends on factors like the type of organic material, desired end products, and energy efficiency considerations. For a business like Georgia Pacific focused on sustainability, corrosion control and utilizing HPC® Coating, understanding these temperature ranges is crucial for optimizing insulation performance to deliver energy efficiency. These benefits collectively enhance operational, financial, and environmental performance.
HPC® Coating is Unmatched in Genuine Savings
HPC® Coating ability to save 49% in energy loss and $332,000 annually per unit at a single Georgia Pacific plant underscores its ability to revolutionize the insulation industry. Despite proven benefits in energy efficiency, corrosion prevention, and personnel safety, widespread adoption of the innovative HPC® Coating coating has been slow, due to resistance to change or existing commitments to poor performing traditional insulation. This raises important considerations about the broader industry’s commitment to energy conservation and sustainability, highlighting the need for embracing more effective insulation solutions like HPC® Coating. When new technology is proven, the effort to change is slowed by status quo attitudes, relationships with current suppliers, acceptance by insulation contractors who are given the role of providing the insulation.
Georgia-Pacific is now using HPC® Coating at other mills following the results of this successful pilot. In addition to the energy savings, HPC® Coating ability to protect manufacturing assets from corrosion adds savings potential for Georgia-Pacific and Flint Hills Resources in millions of dollars in equipment replacement costs. HPC® Coating also improved the quality of the cooking process by allowing the digester to better maintain its internal temperature hence energy savings and quality control.
The potential savings from using HPC® Coating coating at Georgia Pacific could be considerable. If one unit at a Georgia Pacific plant saved $332,000 annually with HPC® Coating coating, and assuming each of the 30 plants has multiple digesters, the total annual savings could be substantial. If we estimate conservatively that each plant has at least one such unit and pipes, the savings across all plants would be 30 x $332,000 = $9.96 million after the single initial investment of application. If more units per plant are considered, or if savings are higher for some units, the total could indeed exceed $20 million annually.
If energy savings are around $9.96 million annually across all plants, the added protection against corrosion could potentially double these savings. This is due to reduced costs in repairs, tear-downs, and replacements. Thus, investing in HPC® Coating not only for insulation but also for its corrosion prevention could lead to total savings exceeding $40 million. The return on investment for HPC® Coating is significant, underscoring its effectiveness in both energy conservation, asset protection and employee protection.
Estimated mathematical progressions for their HPC® Coating application can last over 15 years in the field, $40 million in total savings x 15 years equals $600 million in savings just for one company.
Transforming Industries: Pioneering Energy Efficiency with HPC® Coating
The article highlights Georgia-Pacific’s significant achievements in energy efficiency and environmental stewardship through the use of HPC® Coating (Hot Pipe Coating). The HPC® Coating application at their Naheola mill led to a $332,000 annual energy saving for one digester, contributing to an EPA ENERGY STAR Award. The success with HPC® Coating, which also offers corrosion prevention and safety benefits, points to potential massive savings across Georgia-Pacific’s multiple facilities. It also underscores HPC® Coating potential to revolutionize the insulation industry and the broader commitment needed for sustainable energy solutions.