Super Therm White Paper
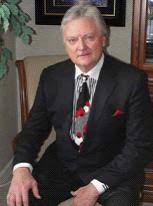
By Joseph E. Pritchett
WATER-BASED, SINGLE COMPONENT CERAMICS HEAT BLOCK THERMAL COATING FOR REDUCING ENERGY
Joseph E. Pritchett is a ceramic researcher and formulator from SPI Coatings (Superior Products International II, Inc.) USA holding a Bachelor of Science from University of Arkansas and Paint Technology courses from University of Missouri. His graduate studies performed with NASA in Huntsville, Alabama, USA and Ceramic Materials research since 1989. He has studied more than 4000 ceramic compounds to determine the type, crystalline structure and size to perform most efficiently for different heat needs.
The purpose of the research was to find which ceramic compounds that could continue to work after being mixed into a paint or coating type formula. Compounds react differently when in dry state versus a wet state and mixed with other compounds.
J.E. Pritchett
Finding the compounds that will continue to insulate when formulated into a coating is the result of 22 years of R&D or simply Trial and Error to find individual compounds that will insulated and then combined together to form a matrix to block radiation waves and detune signals to achieve reduction in “initial heat loads”. This type of insulative technology is not required to have the standard “R” or “K” ratings due to the fact that the heat never loaded to begin the calculation process. You must load heat “before” you can calculate R or K ratings which is simply the measurement of how much and how fast the heat is being absorbed and transferred through a material. If you do not load or reduce the load of heat, you do not have transfer and the R and K value is old technology and terminology.
This technology applies to several products performing insulative techniques for roofing and walls, along with K values are becoming the trend for companies trying to develop new insulative coatings based on thickness with additional products developed for fire controls and to contain heat in pipes and boiler systems. In February 2008, J.E. was a speaker at the 12th Middle East Corrosion Conference in Bahrain on behalf of Saudi Aramco and was a speaker for NASA new technologies concerning the lead thermal insulation coating Super Therm® in Chicago in 1995.
He has developed encapsulation products that are applied directly over rust to reduce prep, time and expense of sandblast with the use of a single coat system. The encapsulation product called Rust Grip® is patented for encapsulation directly over existing rust and directly over bio-hazard materials such as existing Lead-based paint and Asbestos. He has been a NACE member since 2001. He is a current member of the American Society of Naval Engineers. The products have been certified under:
- Underwriters Laboratory
- Factory Mutual
- International Code Council
- US Coast Guard
- DET NORSKE VERITAS
- International Marine Organization
- China National Bureau for the Inspection of Technologies
- China Ship Building Corp
- Japanese Institute of Standards
- Russian Certificate of Standards
- European Standards.
Head Load versus Insulation
Reflective white roof coatings are only good for light reflection. When the coatings became dirty or tarnished, the coatings did not reflect heat.
When Mr. Pritchett worked with the NASA engineers ,he asked the engineers what types of ceramics they would recommend to use in a coating that could provide insulative results. The engineers worked with Mr. Pritchett for some time to choose which ceramics out of the engineering books that would best be successful in blocking heat. Mr. Pritchett tested all the ceramics that were suggested by the NASA engineers and none of the ceramics were successful in blocking heat.
After the unsuccessful testing, the NASA engineers helped Mr. Pritchett by directing him to ceramic suppliers around the world so that he could make contact with them to arrange obtaining ceramic samples and begin a long research and development period of trial and error method of testing each individual ceramic compound to see if it could block heat and repel heat when placed in a coating. During the development processes between 1988-1992, Super Therm® was developed using three ceramic compounds to meet the needs of the heavy industrial plants and petrochemical areas to offer insulation for pipes, tanks and facilities. The first Super Therm® formula was sold for industrial users in 1989. By 1992, Mr. Pritchett had tested over 700 compounds to that date determining which additional ceramic compounds that could be more effective in blocking heat waves. The important point of this testing was to find more effective ceramic compounds that could continue to work to block heat waves even after the coating became dirty and not as white in colour.
In this process of discovery, the R&D process showed that density, crystalline structure and size was the most important characteristics that made the ceramic compound work. The density of the compounds tested and found to block heat would not absorb heat. The density was so low that heat could not absorb into the compound. Metal is easy for heat to absorb into, paper can absorb heat but cannot become hot. The ceramic compounds are 50 times less dense than the paper and therefore, heat cannot load or absorb into it. Crystalline structure is the design of the ceramic compound. This becomes important when the structure is made to repel heat movement over the compound to throw off the heat from the surface. The size is very important to be able to block the radiation wave as it hits the coating surface.
In testing performed by the German engineers, a study was made to determine what materials and at what size is most effective in blocking Infrared radiation or long wave and Visual light or short wave radiation to block the heat wave from entering or passing through the coating. Infrared radiation was tested and determined to represent 54% of the heat from radiation. 43% of the heat was visual light (light spectrum) that heats up the surface and then the surface conducts heat into the building and finally 3% of the heat comes from UV which is not significant. Super Therm® tested to block 99.5% of long wave radiation and 92% of short wave radiation. The ceramic compounds naturally block UV. To successfully block heat waves and heat build-up on a surface, the chosen ceramic compounds perform the functions of blocking heat waves from passing through the coating into the building and other ceramic compounds will block the heat that would normally build up on the surface that would then conduct to the interior.
From 1992-2010, an additional 2900 compounds were tested to find compounds that can improve the existing heat block coatings or develop new insulative coating or high heat coatings that provide answers to insulation problems in industrial environments. In many areas of the industrial complexes or types of operations, fiberglass or rock wool, cannot work well and concrete mixtures are not a good solution. The high temperature coatings developed can be sprayed into place with few man hours, easy to apply, safe to use for workers and the environment and are extremely effective.
A tremendous amount of discovery and testing has been performed since 1989 to determine the best selection of ceramic compounds to provide a total insulative program. From the research used to develop Super Therm®, additional research has continued on ceramic compounds and the combinations of these compounds to find the right balance of ceramics to build other coatings used for high heat insulation as for hot pipes and furnace wall and ceiling uses as well as fire controls for structural steel, apartments, housing and industrial uses to protect all building materials used in construction.
The R&D concept was understood early on that this was the only way to full understand a compound and how it could or would act when mixed into a resin system with water and other raw materials. There are no books written with a study of ceramic compounds and how each functions or fails in all circumstances of wet or where it is mixed into a formula. Therefore, the R&D concept is a daily, weekly, monthly and yearly process on any and all new compounds brought to our attention. The search is ongoing and will continue looking for the next major breakthrough in heat control.
Consider the thickness factor–
Comparing Super Therm® to all the thick insulation materials designed to absorb and slow down the conduction of heat is totally old fashioned, and the promotion to provide the best insulation effort is now due.
Everyone knows that the original insulation materials have been thick materials. The reason is simple: the heat is loaded into a surface and then the materials had to be thick in order to provide time before all the initial heat was loaded and then transferred through the materials to the other side. This conduction method of insulation is gauged by the “R” or “K” value, which is a simple measure of this heat absorption and transfer through the materials. It is a measurement of the rate of transfer.
All the marketing, all the education in the Universities and other coatings companies, all the principles of insulation were based upon thickness to buy as much time as possible from initial heat load to transfer through.
All these thick materials are designed for slowing down conduction – fiberglass, rock wool, foam and newer thermal insulation coatings and materials. These materials accept most HEAT LOAD on the surface which they are trying to work under or next to. All these materials are based on “after-the-fact” heat load, and are doing nothing more than trying to manage the 100% heat load that they cannot fully control.
Now consider Super Therm®. It is not thick and therefore, how could it be effective in conductive resistance? The interesting part of Super Therm® is that it actually works to control two recognised heat transfer modes – radiation and conduction. Since it resist heat load and has a high emissivity, Super Therm® assist the convection heat to balance the interior room temperatures.
NOTE: Convection inside a building moves heat from one location (hot area) to another location (cold area). It works to make the room temperature uniform. The surface properties have little to do with the heat transfer across the wall, i.e. from inside to outside. There is heat load into the wall , then conduction is the mode of transfer to the cool side.
Thick materials were designed to address only conduction, and actually ignore radiation, which is the most dominant heat transfer mode under the sun.
Super Therm® functions to block the initial radiation causing the HEAT LOAD. By blocking 96% of the initial heat load, there is only 5% of heat “available for transfer”, proving that Super Therm® is effective even without the conventional standards of thickness. In addition, Super Therm® provides a barrier against water (Federal Specification) and air movement. It has been studied and proven that a large percentage of heat loss or gain is due to moisture load in the substrate as well as air leakage causing the heat to load quickly and travel through the structure. Super Therm® seals the substrate and blocks moisture load and air leakage.
If you allow only a 4% heat load onto a surface that is the target of insulation, you have only a 4% heat transfer that enters into the substrate. Thick materials allow almost 100% of this heat load because their surface is not designed to block the heat load – they are designed to absorb heat and slowly allow it to transfer – such the “R” or “K” value measurements.
Radiation is not the only heat transfer that Super Therm® blocks. It blocks conduction as well. Blocking HEAT LOAD is the key to measuring insulation and Super Therm® provides the best in the market. It is based and established on all approved test standards.
Marketing and education needs to understand the simple facts of insulation–if you block heat load, you control the amount of heat gain or loss.
Everyone understands the ability of repelling or reflecting heat gain on the exterior. The principle is the same for the interior, as Super Therm®‘s ceramic blend resists the majority of heat load because the
ceramic compounds do not have the density to absorb and hold heat. What heat is absorbed into the coating is thrown back out of the coating to stabilize the heat and helps the convective heat movement between warm and cold areas stabilize quicker.
This is called EMISSIVITY, which is a test measurement of how much a surface can unload the heat it does absorb. Emissivity is a property of a material, not a rate of heat transfer. The material covering the wall or ceiling is Super Therm® and therefore it’s emissivity will equal the rating of the coated surface and not the substrate material. In this case, the emissivity is 0.91 in throwing heat off its’ surface back to the room.
This is HEAT LOAD versus HEAT TRANSFER. Super Therm® blocks heat load, which is the beginning of the heat loss or gain problem. All the thickness designed materials try and control the conduction of the initial heat load that they have no way of blocking. Therefore, the measurement of “R” or “K” relates to how quickly this heat load transfers.
The question becomes, do you want thickness and then more thickness to try to have enough thickness to last for an entire day of heating before that heat can make it to the cool side? This rate of heat absorption is accelerated with any small absorption of moisture (humidity) and air flow. When any of the thick materials absorb as little as 1 1⁄2% of moisture (breathing on it), immediately kills as much as 30% of its’ effectiveness and accelerates the speed of the heat conduction through the material.
Expand the expectation for Super Therm® from just being a heat control, whether that be a summer heat gain or winter heat lost, to a more complete system coating that can not only be a moisture barrier, but a proven water barrier to a 100 km/h wind driven rain, a sound barrier blocking up to 50% of the talking frequency sound transmission through walls (due to the same ceramic using low density compounds that cannot load heat), to a “0” fire spread giving a Class A rating, to a mould/mildew blocker and helping to stop condensation, yet can breathe to avoid mould development.
This is simply the reason for opening our minds to new technology that works to address the causes of lost or gained heat and not just on one part of heat control called “conduction”.
Examples of test results from Florida Energy Office and other companies:
Super Therm® Energy Industry Test Reports
Super Therm® is an innovative and effective energy conservation measure (ECM). SPI Distributors undertook testing with its industry partners associated with the Florida Energy Conservation Assistance Program in 3 different locations.
- Florida – July 2003 (pdf / video) – 20-30% Reduction
- Denver – February 2004 (pdf / video) – 26-30% Reduction
- Texas – August 2006 (pdf / video) – 46-52% Reduction
The results of each report were outstanding with regard to Super Therm‘s energy efficiency gains due to reduced BTU’s. Super Therm® has a 99% BTU rating, means it blocks virtually all Infrared heat entering a structure. This is the only product of its kind that makes it a true solar heat block coating, not a reflective paint.
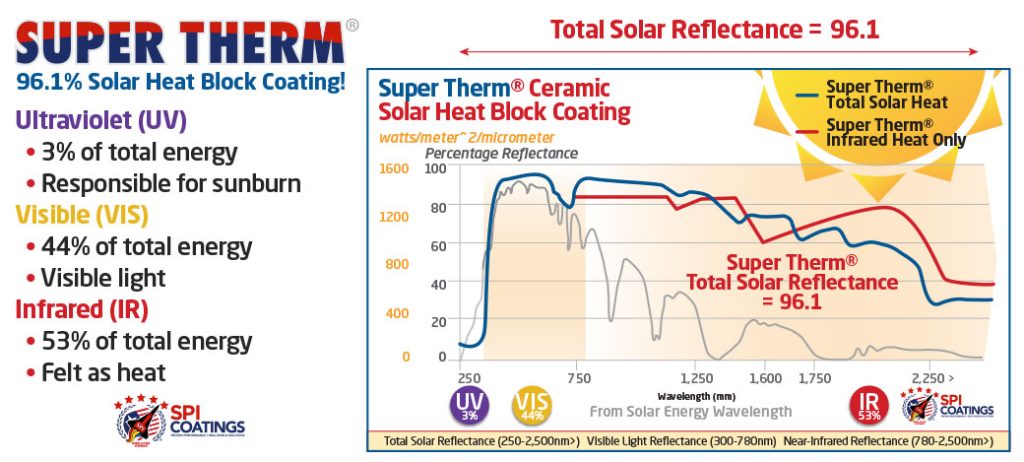
Florida
20-30% Reduction
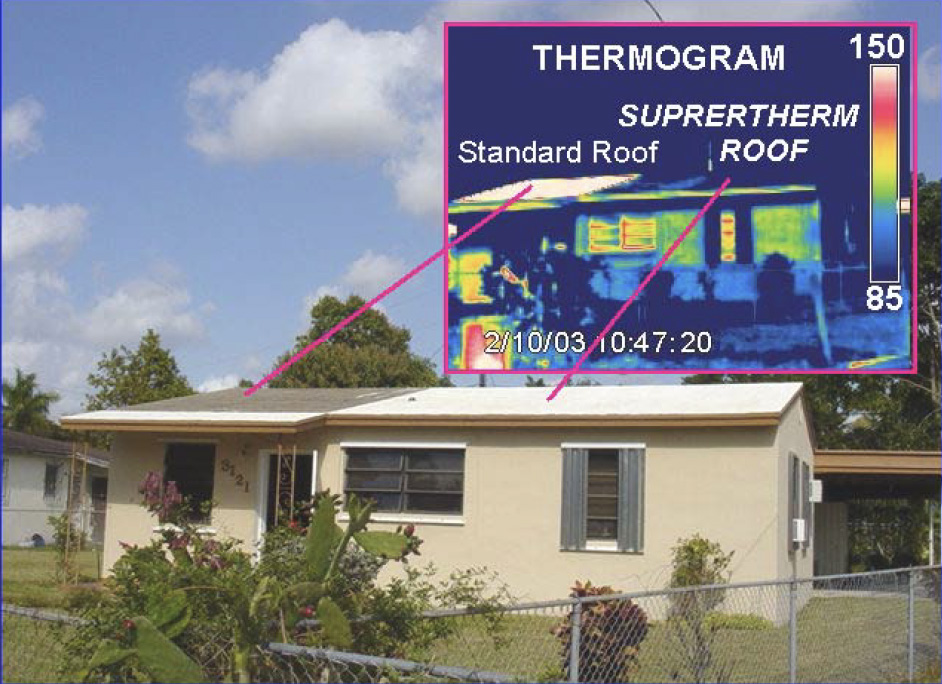
- Pay back of approximately 2.2 years
- Reduction from Super Therm Solar Heat Block coating: 133,100 BTU’s per hour
- Super Therm® reduced total Roof Solar Gain Loads by 20 to 30%.
On February 10th & 11th, 2003 a test was conducted on Super Therm® Ceramics Thermal Coating, applied to a residential home roofing system located in Dade County, Florida in accordance with the State of Florida Energy Office / Energy Conservation Assistance Programs Designation: ECAP-CUL-1-99
Test Method for Comparing Utility Loads in Standard Constructed Buildings.
The objective of this procedure is to determine the actual impact on a facility, after the implementation of a Energy Conservation Retrofit and verify the reduced utility loads, if any, in occupied residential, commercial and government buildings. The focus of this procedure is to provide a comparison to known standards for all parties interested in using energy related products to displaced conventional utility loads. This procedure addresses the energy consumption properties of the equipment and structural envelope tested.
Our testing indicated that your application of Super Therm® reduced total Roof Solar Gain Loads by 20 to 30%. This would qualify as an effective Energy Conservation Measure (ECM) fundable with Federal and State of Florida Energy Grant Dollars where applicable.
Predicated on historically accepted Florida Air Conditioning building component load data (see pdf) and the square footage of the project surveyed, the estimated air conditioning load reduction from the Super Therm® retrofit was approximately 11.09 tons of load per 24 hour period.
- Standard Roof load with no insulation coating: 226,000 BTU’s per hour
- Super Therm Roof load: 93,500 BTU’s per hour
- Reduction from Super Therm solar heat block coating: 133,100 BTU’s per hour
- Reduced environmental impact 66 pounds of power plant emissions per hour
As installed, at the time of this testing, the Super Therm® Roof Coating System proved to be an effective Energy Conservation Measure (ECM) that produced a reasonable simple pay back of approximately 2.2 years on this particular project. This would indicate that it’s application could be fundable with Federal and / or State of Florida Energy Grant Dollars where applicable.
On behalf of the The State of Florida Energy Office and the United States Environmental Protection Agency, let me thank you for your efforts in developing an affordable product that obviously can be instrumental in Conserving Energy. We hope you will continue to consider Florida as a valuable market for your products. See the full report PDF.
NOTE: Laboratory and Field project results as stated here may vary according to different climate conditions.
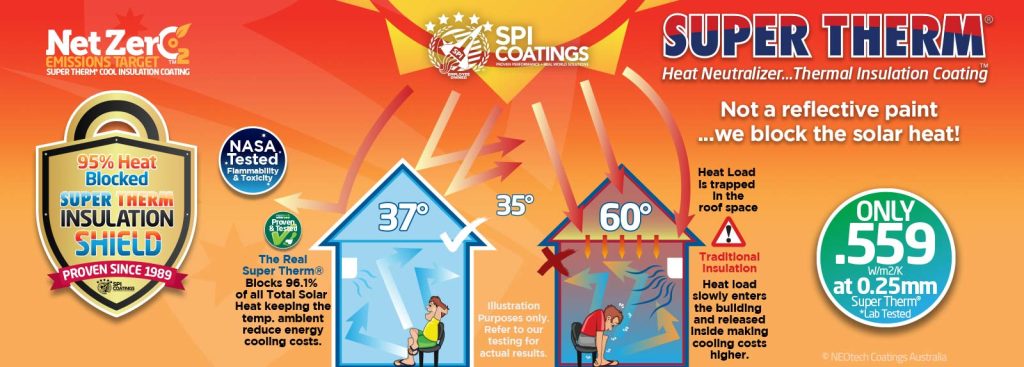
Denver
26-30% Reduction
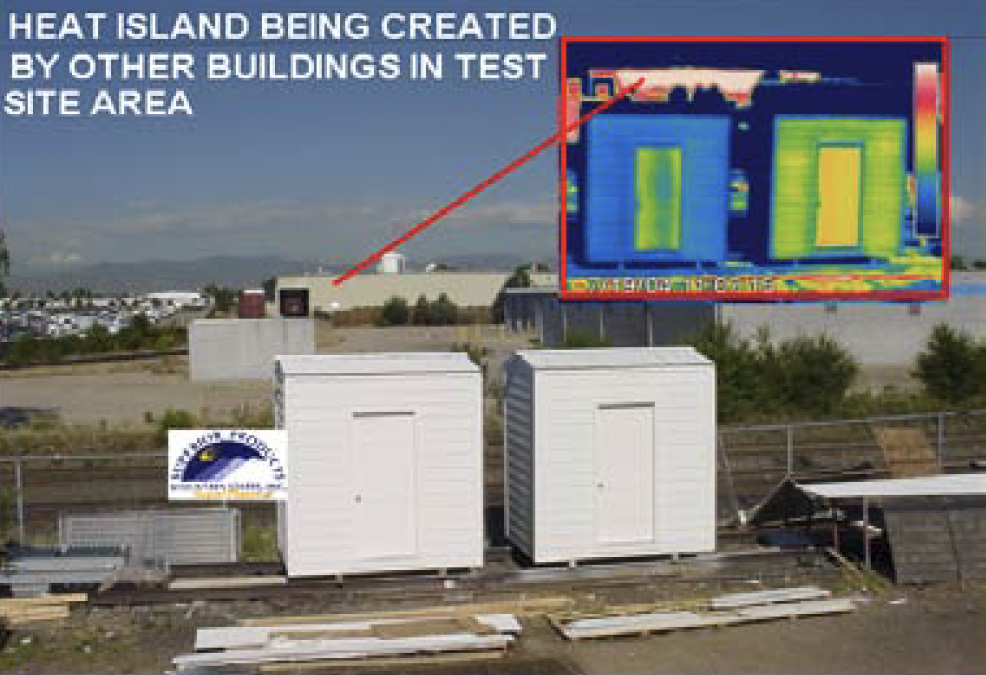
- A 26 to 30% overall increase in energy efficiency
- Reduced Heat Island Effects taking place in most urban areas
On July 19th & 20th, 2004 in accordance with the State of Florida Energy Office / Energy Conservation Assistance Programs Designation: ECAP-CUL-1-03 Method for Comparing Utility Loads in Standard Constructed Buildings in Denver, Colorado.
The objective of this analysis is to determine the impact of the “As Built Conditions and As Installed Components / Equipment” on the utility loads in occupied residential, commercial and government buildings. The focus of this procedure is to provide a comparison to known standards for all parties interested in using alternative energy devices to displaced conventional utility loads. This report reflects the performance characteristics of Super Therm®, as applied to the test facilities external surfaces, as a possible passive Energy Conservation Measure (ECM) to reduce internal Energy Loads and reduce the Heat Island Effects caused by roofing systems in urban areas.
The location of the test specimens was adequate. Both buildings were of standard construction consisting of wood framing, standard OSB wall and roof sheeting’s with a standard galvanized metal roof covering and James Hardey Board external wall coverings. The calculated R-Value of the uncoated existing materials was found to be approximately an R-2.45. The only difference between the two buildings consisting of approximately 48 square feet of control zone area was the external protective coatings.
One of the buildings was coated with a standard white latex paint while the other buildings roof and all external surfaces, including the front door had been coated with Super Therm®. As noted and some of the test results this report the differences created by Super Therm® concerning load reductions produced by thermal conduction, convection and absorption were significant. Additionally, significant reductions in moisture infiltration were also noted.
Our survey indicated that the test specimen’s building envelope related energy loads were reduced approximately 26 to 30% by the use of this particular Energy Conservation Measure (ECM). This was accomplished with no negative effect on the existing buildings Architectural Aesthetics.
Our Energy Flow analysis using a simulated water flow rate of approximately 6.5 gallons per minute indicated that the standard constructed building would require a minimum of 1,037 BTU’s of heating or cooling energy per square foot to maintain a minimal comfort level.
In retrospect, the building coated with Super Therm® reduced these loads to 766 BTU’s of heating or cooling energy per square foot to maintain the same minimal comfort level. This relates to a 26 to 30% overall increase in energy efficiency depending on the percentage of direct solar gain.
While on that subject, our office feels that particularly when addressing external building thermal loads, your product could significantly reduce the Heat Island Effects taking place in most urban areas. The photo and Thermogram below clearly show the benefits provided by your product in this arena.
This is the second time we have had the pleasure to test your product, it is rare that a single product will show such Repeatable Results in two totally different environments, South Florida and Denver Colorado, a true testimonial to your products ENERGY STAR rating. See the full report PDF.
NOTE: Laboratory and Field project results as stated here may vary according to different climate conditions.
Texas
46-52% Reduction
Shipping Containers
- Conduction related energy loads were reduced approximately 46 to 52%
- Internal surface temperatures: 20°C (37°F) Cooler
- Outside Surface Reflectivity: 50% Higher
- Ultraviolet absorption rate: 92% Less
- Internal Moisture levels: 28.5% Dryer
On August 23rd & 24th, 2006 a test was conducted in LaPorte, Texas in accordance with the Florida Energy Conservation Assistance Programs Designation: ECAP-CUL-1-03 Method for Comparing Utility Loads in Structures and Buildings.
The objective of this analysis is to determine the impact of the “As Built Conditions and As Installed Components / Equipment” on the energy producing loads on occupied residential, commercial, government building and other structures. The focus of this procedure is to provide a comparison to known standards for all parties interested in using alternative and conventional conservation products and devices to displaced energy loads. This report reflects the performance characteristics of Super Therm®, as applied to the structures external surfaces, as a possible passive Energy Conservation Measure (ECM) to reduce internal Energy Loads and reduce the Heat Island Effects caused by exposed surfaces in urban areas.
Our data indicated that at the time of this survey the test specimen container inside surface conduction related energy loads were reduced approximately 46 to 52% by applying Super Therm® as an Energy Conservation Measure (ECM) to outside surfaces.
Average site weather conditions during the analysis period were as follows:
- High Temperature 36°C (97°F).
- Low Temperature 23°C (74°F)
- Average Wind Speed 2-4.7 knots (3 to 5.5 MPH)
- Average UV intensity 99 A+B
Outcomes:
- Inside container ambient temperature: 12°C (22°F) Cooler
- Thermal conductance to outside environment: 50% Less
- External surface temperature: 26°C (47°F) Cooler
- Internal surface temperatures: 20°C (37°F) Cooler
- Outside Surface Reflectivity: 50% Higher
- Ultraviolet absorption rate: 92% Less
- Internal Moisture levels: 28.5% Dryer