Abattoirs and Stockyards
Abattoirs and stockyards can be challenging environments for many reasons. Many areas of the stockyards and abattoirs are effected by heat, corrosion, chemicals and wear and tear. This places increased cost and maintenance pressures on the business operations of any facility. Areas that can be effected include:
- Liquid waste – (Moist Metal Grip, Lining Kote, Enamo Grip)
- Cooling Efficiency and Thermal Barriers – (Super Therm)
- Cost of corrosion – (Rust Grip, Moist Metal Grip, Lining Kote, Enamo Grip)
- Steel – (Rust Grip, Moist Metal Grip)
- Grain storage and handling – (Moist Metal Grip, Super Therm)
- Underground Tanks – (Moist Metal Grip, Lining Kote)
- Pipelines – (Rust Grip, Moist Metal Grip, HSC, HPC)
- Boiler feedwater quality – (Rust Grip, Moist Metal Grip, HSC, HPC)
- Fences – (Rust Grip, Enamo Grip)
- Surface protection and repair – (Rust Grip, Moist Metal Grip, Lining Kote, Enamo Grip)
- Races and Processing – (Rust Grip, Moist Metal Grip, Enamo Grip)
- Support columns – (Rust Grip, Enamo Grip)
- Cattle crush construction – (Rust Grip, Enamo Grip)
- Fuel tanks – (Rust Grip, Lining Kote, Enamo Grip)
- Sheds and Roofing – (Rust Grip, Super Therm)
- Chemicals – (Rust Grip, Moist Metal Grip, Lining Kote, Enamo Grip)
Rust Grip, Moist Metal Grip, Lining Kote and Enamo Grip
Super Therm, HSC and HPC
Liquid Waste
Livestock produce large quantities of liquid and solid waste. Solid wastes include fresh manure, decomposed manure (from the yard floors and in stockpiles). Liquid wastes include urine, washdown and contaminated by products from stockyards. Both types of waste are high in degradable organic matter, nitrogen, phosphorus, micro-organisms, and may contain pathogens, pesticides, antibiotics and other pharmaceutical residues. These are harsh chemicals that are particularly aggressive on metal infrastructure and the potential affects include:
- Corrosion
- Higher maintenance
- Potential contamination
- Increased running costs
This applies to permanent stockyards for confining and holding livestock for a range of purposes including sale, receival, transport, emergency feeding, husbandry, weaning, rendering, slaughtering and similar food or hide production animal facilities operating for a commercial purpose. It includes stockyards that are used both continuously and occasionally.
Traditionally new steel components are hot dip galvanised and rust proof. During galvanising each yard component is cleaned in acid to remove all traces of scale or rust, then dipped in galvanising zinc, coating it completely in places unreachable by spray or powder coating. Galvanising can be a toxic process which is why the innovation of Rust Grip, Moist Metal Grip, Lining Kote and Enamo Grip deal with the harshest environments with proven results.
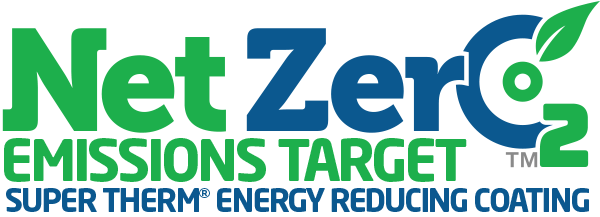
Cooling Efficiency and Thermal Barriers
The other aspect of abattoirs and stockyards is with regard to thermal protection and cooling energy efficiencies.
- cool rooms
- transport of processed material
- steam pipes
- administration buildings
With the focus on both energy efficiency and net zero target emissions, having the advanced technology that provides thermal benefits is an important aspect of running and efficient abattoir. The ability to reduce cool room costs with the reduction of solar heat load creates energy savings and cooling costs. The ability to reduce heat loss from steam pipes ensures more heat is contained in the pipes and reduces the risk of CUI. Our coatings like Super Therm, HSC and HPC manage better thermal efficiency and employee safety.
Cost of corrosion
Addressing corrosion not only cost effective, it can help prevent accidents. However, decision makers do not always realise what a big issue corrosion will be, or how they can prevent it. An appreciation of corrosion will, in many cases, provide opportunities for its threat to be removed during the design stages of a project, or a successful treatment program to be implemented.
The key to avoiding undue corrosion in your industrial workplace is choosing materials that will handle the conditions and planning. NEOtech Coatings can help with this, as we offer a range of products that stop corrosion and resist significant corrosive or harsh environments. Corrosion is a challenge for many industries including the meat and livestock industry. The effects of corrosion present a huge financial cost and can lead to potentially hazardous mechanical or structural failures.
But it does not have to be this way, as much of this corrosion can be prevented through awareness and good protection. By covering metal with leading coatings prevents it from interacting with the air or other substances in the environment that cause corrosion. This also has the potential for aesthetic appeal.
Steel
Long-lasting surfaces. Galvanised or well-protected steel is hard wearing. Weight for weight, steel is stronger than concrete. Carbon steel and stainless steel equipment including pipelines, piping and storage tanks face significant challenges from Microbiological Induced Corrosion.
Grain storage and handling
Wet grains, ground processed grains and chemically treated grains can corrode standard carbon steel fabrications. Each grain type to be handled must be checked to determine if stainless steel is needed, or will reduce possible life cycle costs. If water wash down, or cleanin-place systems are required, materials used for fabrication in the distribution system should be considered.
Regardless of its type of construction or location, the tank must have adequate vents. This is to minimise condensation (which causes corrosion in steel tanks), vent fugitive emissions and prevent a vacuum being drawn on the tank by pumping.
Underground Tanks
Underground LP gas storage tanks must be at least 3m from underground tanks used to store flammable and combustible liquids although this can be reduced to 1m if a specifically designed, compatible corrosion protection system that caters for the area between the tanks is provided. Other separation distances also apply (see AS /NZS 1596).
Pipelines
So many causes of pipeline corrosion – even on new pipelines! Increased corrosion potential on these pipes that have spent years in outdoor storage yards is a concern. Stockyards are an essential facility for raising beef cattle, sheep and pigs. Once built they last for many years. New yards are expensive so take care to ensure minimal maintenance and future operating costs by selecting the best plan and materials for your enterprise.
The main difference between a yard designed for 200 head of cattle and a yard for 2000 head is the size of the receiving and holding yards. Excessive capital expenditure on sturdy yard fences can be reduced by having several small holding paddocks which enable the stock to be worked in smaller groups. Most yards require facilities for receiving, holding and moving cattle into smaller working yards for drafting, animal restraint, loading and unloading. Calf branding facilities are required for breeding herds, whereas a dip may be necessary in cattle tick infested country.
In acid soils, steel yards should be coated to about 300 mm above ground level. A cement collar above ground line should also be added to reduce corrosion from soil buildup around the posts. Painting of steel work in cattle yards is important. It is also a significant additional yard construction cost and needs to be considered from a maintenance point of view.
Boiler feedwater quality
A steam boiler plant must operate safely with maximum combustion and efficient heat transfer, and this is profoundly affected by the quality of the water used to produce the steam in the boiler.
Boilers need to operate under the following criteria
- Freedom from scale – hard water will cause scaling of the heat transfer surfaces and make frequent cleaning of the boiler necessary
- Freedom from corrosion and chemical attack – water containing dissolved gases, particularly oxygen, will corrode the boiler surfaces, piping and other equipment
If the impurities in the boiler feedwater are not dealt with properly, they will be carried over into the steam system and cause problems such as:
- contamination of the surfaces of control valves and heat transfer surfaces
- restriction of steam trap orifices.
Fences
Steel pipe is probably the most common material for fence line posts. Cables should be attached to, or directed through, fence posts so that no sharp edge can deteriorate the cable as it moves constantly back and forth under pressure from the cattle. Cable wear, corrosion and ongoing maintenance are important considerations in deciding the most practical applications.
Cables passing through steel fence posts need a steel sleeve to reduce fraying. Sleeves prevent water entering the hollow post but can accumulate moisture which accelerates corrosion of the cable. This is an expensive fabrication technique.
Columns are commonly made from steel but the base should be encased in concrete to prevent corrosion, to provide better protection from equipment damage during pen cleaning operations and to reduce injury to cattle that bump into them.
Local thickening of concrete around the posts, or having the posts on the outside of the feed bunk, will make it difficult to clean around them to remove manure that has built up against the bunk wall and to clean along the feed trough apron. Posts that are cast into the concrete wall need to be treated with epoxy or equivalent to prevent corrosion at the steel/concrete joint and subsequent failure.
Posts cast into the concrete wall need to be treated with epoxy to prevent corrosion at the concrete joint. Most fencing panels in soaking yards are made of steel. Corrosion resistant material such as stainless steel may increase longevity of posts in fence lines, especially if using recycled water, but is expensive
Surface protection and repair
Some ration ingredients, particularly silage and molasses, will corrode steel and iron in concrete reinforcement, and concrete surfaces. Sealing the inside of the feed bunk with two-component epoxy resin will protect the surface from chemical attack and abrasion. As with all coating applications, surface preparation is critical. Epoxy is best applied when the bunk is new. The surface must be dry and free of dust and surface contaminants (such as oils or chemicals) before application.
Typically, two or more coatings will be required, and this protection will need to be renewed periodically as the original surface wears. Feeding systems for further information on the use of coatings to protect the surface of concrete against corrosion and wear.
Races and Processing
Corrosion is a major consideration if wash-down water has high salt content. Construction material types and surface metal finishes can help inhibit or reduce the rate of corrosion. Corrosion is a major problem and use of a more durable material and finish can help slow this. In an attempt to measure the actual conditions experienced by cattle, some feedlot managers have placed weather stations inside a pen or cattle alley. However, pen conditions can be extremely aggressive and can result in corrosive attack by organic matter.
Support columns
Where possible, clear span structures are preferred. Columns should not be placed inside pens other than in line with fences. No columns should be placed on the alley side of feed aprons or troughs. Columns should be encased in concrete to a height of approximately one metre (1m) to prevent corrosion around their bases and damage from pen cleaning equipment.
Cattle crush construction should also ensure
- Quiet operation by limiting undue noise (such as from a metal floor)
- Minimal dirt build up (thus reducing corrosion)
- Ease of cleaning
- Moving parts are physically easy to operate and guarded for operator safety
- Ease of maintenance with accessible greasing points
- Railing that is strong, yet quiet when knocked by cattle
- Rust prevention measures, such as galvanising, undercoating and anti-corrosive paint
- An ability to add additional items (e.g. load cells, chin lifter, automated vaccination or drenching mechanisms).
Fuel Tanks
Tanks must be of sound construction and suitable for filling with petroleum products. This means that there are no signs of leaks, or major deformations of shape (cracks, dents). For tanks with supporting structures, these deformations will move the tank’s centre of gravity and will also establish stress points where corrosion will occur more rapidly, or stress the supporting framework.
All fittings on the tank must be in good condition and free from leaks. If a dispensing hose and nozzle is fitted, it should have an isolation valve at the tank outlet. There must be no corrosion that could materially affect the tank’s integrity. As with supporting structures, rust can have a major impact on the soundness of a fuel tank. The degree of damage caused by rust is dependent on the thickness of the steel used in the tank’s manufacture, and the depth of the rust has penetrated. AS1692 outlines the minimum thickness of plate used in tank construction with which current manufacturers of fuel tanks comply.
Areas at particular risk of rust damage are:
- top of tanks, especially if they are cylindrical tanks mounted vertically (on end)
- underside of tanks
- fill point, outlet and drain plug
- welded seams
- surfaces and joints between the tank and the support structure.
Maintaining the integrity of the fuel being stored
To keep water out of the tank, install a desiccant breather to remove moisture and airborne debris from air drawn into the tank as fuel is removed. Turning over fuel frequently minimises moisture problems and microbes. Hence, tanks should be sized to meet the needs and contingency requirements of the feedlot. Minimising temperature extremes also minimises condensation (and microbial growth). To maintain fuel quality and reduce losses, install fuel storages out of direct sunlight (but not under trees) and paint them a light colour if possible. Installing storage tanks on a slight gradient allows water and sediment to collection at the low end and be removed.
Sheds and Roofing
Australia is well serviced by companies that design and construct all types of farm buildings. Cost will depend on geographic location, source of supply, span and length of the building and the way in which the project is undertaken. If the shed frame is made from steel poor construction or inadequate maintenance may lead to corrosion problems with steel. Galvanised steel sheeting is the most common and most economical form of cladding yet creates unknown issues with regard to increased thermal heat load from the sun. In fact galvanised steel has a very high solar absorption and very low emissivity (heat release). Super Therm® blocks the solar heat and therefore adds more protection, safer environment and long term corrosion protection.
For single row shed design, a mono-slope roof is adequate. Monoslopes are most identifiable by their sloped roof or truss. The pitch of the roof has an effect on ventilation, water carrying capacity of the roof area and lifespan. Typically with a steeper roof, more debris is washed off the surface during rain events, improving its effective lifespan. The lower the span the more heat is also absorbed and an energy reduction ceramic cool coating of Super Therm® will protect both the roof and walls from unnecessary solar heat absorption and heat load.
Chemicals
In addition, copper, gold, lead, silver, zinc and other desirable metals are often found in ores rich in iron sulphide. When iron sulphide is exposed to air or dissolved oxygen in water, the sulphide oxidises to sulphate, which then turns to sulphuric acid (H2 SO4). Sulphuric acid is a highly corrosive chemical. It is also one of the primary constituents in acid rain and is toxic to most living organisms. The sulphuric acid produced in sulphide mine tailings makes the surrounding water more acidic. In addition to the direct effects of that acidity, acid water leaches toxic heavy metals from the tailings into receiving water bodies.
Leakage of fluids from damaged or corroded chemical storage systems.